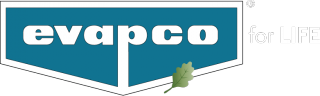
Superior Quality as Standard
Decades of engineering know-how and innovation has placed EVAPCO at the forefront of evaporative cooling technology. This same level of expertise and commitment to excellence is applied to every stage of the design, development, and manufacturing of our dry and adiabatic products.
Coil Design
Through the use of computational fluid dynamics (CFD) modeling software, finite element heat transfer analysis, and proprietary coil performance calculation methods, EVAPCO engineers have identified significant design elements to improve the finned coil performance. The extensive computer modeling has been refined and verified through coil performance evaluation in EVAPCO's state of the art research laboratories.
Superior Stainless Steel Technology
eco-Air Series units are constructed with high-grade Type 304L stainless steel tubing and aluminum fins as standard for both maximum durability and heat exchange. The stainless steel tubing meets the requirements of ASME B31.5 refrigerant piping code. The tubing is roll formed and continuously welded, annealed, and tested using an eddy current device. The round tubing is fit into the aluminum fin plate and hydraulically expanded. This procedure provides more consistent contact between the tube and the fin plate than mechanical expansion. The entire coil is then pressure tested to 110% of design working pressure. Lastly, the coil is dried, evacuated, and charged with low-pressure nitrogen prior to shipment.
EVAPCO’s stainless steel tubes are available in 5/8-inch OD. Coils are built in 6, 8, 10 or 12 FPI as standard using a full-collar aluminum fin. Multiple fin thicknesses are available to accommodate a range of industrial applications.
For applications where corrosion of the aluminum fin is a concern, EVAPCO offers pre-coated epoxy fin stock with no reduction in thermal capacity.
Reduced Maintenance
Scaling, corrosion, and water born bacteria concerns are minimized or eliminated with dry and adiabatic cooling equipment. The eco-Air Series reduces the maintenance traditionally associated with fully evaporative systems. The eco-Air adiabatic condenser is designed as a once through system, meaning it has no pump and no basin to hold water, which further reduces the time required for maintenance. Additionally, the adiabatic pads filter the air before reaching the coil, limiting the exposure of dirt and debris to the tube and fin heat transfer surface. Both NEMA and EC motor options require zero routine maintenance. There are no bearings to grease, belts to adjust, or fans to pitch and balance.
Factory Mounted and Wired Controls
The motors on the eco-Air series are pre-wired at the factory to UL standards, reducing costs associated with field wiring. As standard, all units are wired to a common terminal box. Adding the EVAPCO controls package allows for both single point power supply and complete capacity control.