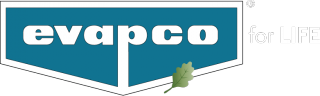
Automation and Autonomy Reduces Cooling Tower Maintenance
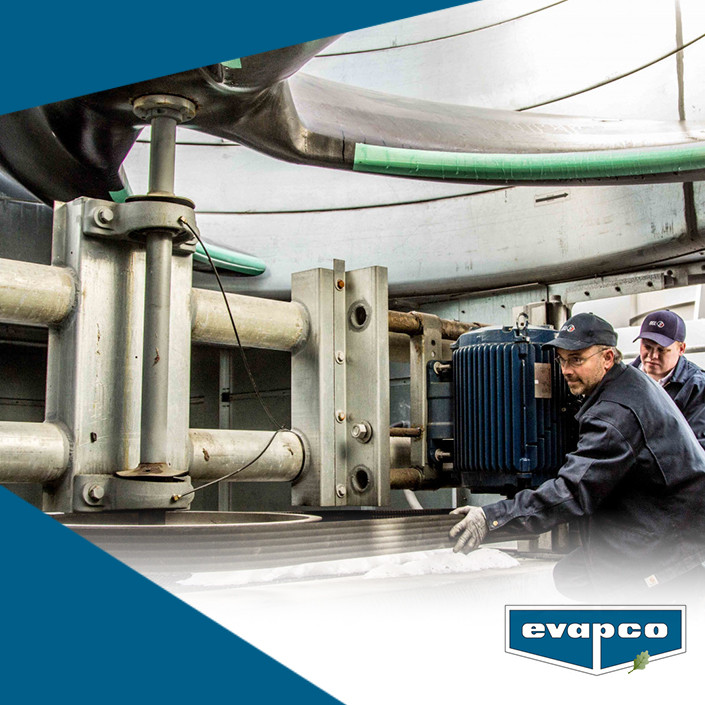
For decades, cooling towers have provided the most efficient means of cooling large commercial buildings or industrial process loops by supplying the lowest operating temperatures.
Yet, through the years, water-based cooling systems have evolved dramatically. Terminal units, chiller plant components, cooling towers (and fluid coolers), and the controls that tie them together have all made strides in efficiency, controllability, heat transfer and water conservation. The end-user, owner, installer and maintenance personnel all benefit.
“Many facets of tower maintenance are still best conducted manually and with a predetermined schedule, but automation and autonomy have found a place in cooling tower and closed-loop fluid cooler systems,” says Kevin Hetman, who operates Chesapeake Systems’ Mr. GoodTower division. “Mr. GoodTower’s function is to repair cooling tower systems more than to maintain them, so we’re very familiar with the fallout of ineffective maintenance. If more elements in the maintenance process are handled automatically, the healthier the system will be.”
The level of maintenance a specific cooling tower requires is largely determined by the quality of makeup water available at the site and how system fluids are treated. In recent years, both makeup and recirculating water treatment have been simplified. EVAPCO, a global manufacturer of cooling towers, fluid coolers and dry and adiabatic coolers, has addressed the need for streamlined water treatment. “Our three most recent water treatment developments include solutions for both makeup water and recirculating water, all while greatly reducing the labor and mess that can be associated with conventional chemical treatment,” explains Brett Alexander, applications engineer at EVAPCO.
To read the entire article, please visit: PHCP PROS